Prevention of ocular injuries
The most striking advances in safety during the last century have been made in industry, the frequency rate for injuries dropping significantly in this time. This reduction has been due to a greater awareness of the hazards which exist and a greater co-operation between management and specialists in the fields of safety engineering, industrial hygiene and industrial medicine, in reducing the hazards inherent in the equipment and working methods, and in educating the employees in basic principles of accident prevention.
In the 19th century, the safety of the employee was generally considered to be his own responsibility, with little liability being placed on the employer. Throughout the years it became accepted that management should do more for the safety of its employees and soon various laws came into existence in which the employer should accept primary responsibility for injuries incurred at work and should take every step possible to safeguard his workers.
As a result, claims for compensation, fines and obligations to provide benefits during time lost from work, as well as indirect costs from interruption of production, made it worthwhile for employers to invest in accident prevention programmes and to follow basic safety procedures which include:
- identification of the risks and evaluation of their significance;
- seeking to eliminate hazards and causation factors;
- designing machines and procedures to reduce the hazards;
- minimising their effects by the provision of appropriate protective equipment to prevent injury or reduce the severity;
- taking measures to ensure that the equipment is used by the worker on every occasion on which he is exposed to risk.
Protection through engineering and equipment design is generally more reliable than through methods depending on human behaviour. The use of personal protective equipment becomes imperative, however, when hazards are impossible to control by other methods, and this is particularly so when there is a risk of injury to the eyes.
There are no such things as minor eye accidents. The smallest abrasion can have the most disastrous results if neglected, leading to serious infection or even loss of sight and, it appears that the majority of these injuries could have been prevented. While in the past eye injuries have been associated with industrial occupations, there are an increasing numbers occurring in sports and leisure activities and at home.
Obviously the number of eye injuries caused by industrial accidents varies according to the level of industrial activity in the area and, sadly the incidence of such accidents does not appear to be reducing.
Recent surveys into the causes and types of ocular injury of people admitted to hospital to show that, every year, thousands of people sustain eye injuries as a result of their work. The figures, of course, often only cover the more serious reportable accidents. Literally tens of thousands of accidents to the eyes go unreported and are dealt with on a first-aid basis.
In 1985, a large study by Chiapella and Rosenthal examined the clinical records of 6,576 patients admitted to the eye casualty department at Leicester Royal Infirmary during a one year period. As may be expected, the majority of patients were men in the 20-40 years age group, and the main cause of eye injuries were foreign bodies. The Table shows the main occupations of the patients in whom the injuries occurred, with press and machine tool operators the most likely to suffer injury (32 per cent). It is important to note that most of the occupations listed are known to have potential ocular hazards, and that eye protection should have prevented injury. The study suggests that eye protection was either inappropriate or was not being used correctly by the workers.
Table 1 Main occupations of patients in whom ocular injuries occurred (reproduced from Chiapella A.P. and Rosenthal A.R. (1985) One year in an eye casualty clinic. Br J Ophthalmol, 64, 618-625)
|
Number of Cases |
Occupation |
All injuries |
Burn |
Contusion |
Foreign body |
Corneal Abrasion |
Press or Machine Tool Operators |
484 |
13 |
13 |
425 |
64 |
Motor Vehicle or Aircraft Mechanic |
147 |
10 |
7 |
111 |
18 |
Metal Worker |
145 |
7 |
4 |
111 |
27 |
Construction |
131 |
16 |
6 |
82 |
37 |
Sheet Metal Worker |
124 |
3 |
3 |
108 |
12 |
Electrician |
104 |
5 |
3 |
77 |
24 |
General Labourer |
120 |
6 |
5 |
79 |
34 |
Welder |
97 |
9 |
3 |
72 |
18 |
Bus, Coach or Lorry Driver |
76 |
4 |
5 |
46 |
23 |
Others in Processing |
51 |
4 |
1 |
23 |
8 |
Painter & Decorator |
44 |
7 |
1 |
23 |
17 |
The need for eye protection in many industrial processes had long been recognised for a number of obviously dangerous jobs.
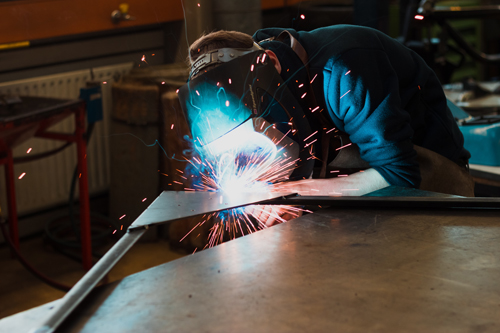
Photo by Maxime Agnelli on Unsplash
For example, blast foundry men, welders and people engaged on certain chemical processes, have been required by law to be provided with suitable eye protection. Later it was recognised that there were many jobs where the hazards were less obvious and for this reason perhaps more dangerous, where effective measures needed to be taken to reduce the appalling number of eye injuries and the disastrous consequences which occurred as a result.
In the United Kingdom, in 1975, as part of the Health and Safety at Work Act 1974, the Protection of Eyes Regulations came into effect, similar regulations already being in force in the United States from 1971.
Subsequent amendments have resulted in six new Regulations:
- The Management of Health and Safety at Work Regulations 1992
- The Personal Protective Equipment at Work Regulations 1992
- The Workplace (Health, Safety and Welfare) Regulations 1992
- The Provision and Use of Work Equipment Regulations 1992
- The Health and Display Screen Equipment Regulations 1992
- The Manual Handling Operations Regulations 1992
Employers are now required to identify and assess the risks to health and safety present in the workplace, so that the most appropriate method of reducing the risks to an acceptable level can then be decided. The regulations state that the provision of personal protective equipment (PPE) should be viewed as a last resort and that risks should be controlled by other means wherever possible.
The Personal Protective Equipment Regulations 1992 cover eye protectors and it is the responsibility of the employer to make sure that they are appropriate for the risks concerned.
The employer must:
- Identify the hazard(s) present, such as chemicals, flying particles or radiation sources
- Assess the degree of risk, for example, the probable size and velocity of any flying particles
- Select a suitable type of PPE from the range of ‘CE’ marked equipment (indicating that the equipment has a certificate of conformity)
- Ensure that the PPE fits correctly, after adjustment, if necessary
- Ensure that, where more than one type of PPE is necessary, they should be compatible and still effective against the risks
Safeguarding the worker’s eyes may involve the provision of protection in the form of masks, visors, goggles and spectacles (including those incorporating impact resistant prescription lenses for those normally wearing spectacles), or other eye protectors according to the risk factor of the particular job. Minimum standards of quality and protective potential of both lenses or eye-piece and housing to which protective appliances must conform are laid down by UK legislation and European Community directives.
Whilst it is not possible to give guidance on appropriate eye protectors for each and every hazard, it is of utmost importance to ensure that they are:
- suitable for the person for whose use they are provided. In other words, well adapted for the process and well adapted for the wearer in that they must fit properly;
- appropriate in design and quality for the risk against which they are intended to protect, and marked to indicate their purpose. Some eye protectors are designed for special purpose, for example, to withstand high impact, chemical splashes, fumes, and so on. It would be considered inappropriate to use protective spectacles which are not intended to afford protection against such risks, unless worn in conjunction with other protective devices so designed;
- used by the person exposed to risk, taken proper care of by them and that such persons notify any damage or loss of the eye protector.
Even the most ideal safety appliance is effective only when used properly, and this is especially true of eye protectors. If eye protection is not comfortable it will not be worn. It must fit well and to do its job effectively, it must not slip down, fall off or interfere with the freedom to work. It is also necessary through continuous propaganda to persuade employees to make full use of them on every occasion on which they are exposed to risk.
Accidents and defective vision
There has been a considerable amount of research supporting the relationship between accidents and defective vision. Vision screening carried out in a large steel works showed that employees who did not come up to the visual standard laid down were found to have experienced, on average, 20 per cent more accidents than those who were visually efficient.
An investigation in a paper mill studied two groups of workers whose accident records for the previous year were known. One group was of 52 men, each having at least one serious accident. Fifty-two accident-free workmen comprised the control group, age, experience and service time being carefully matched for the two groups. Out of a total of 104 persons, 59 came up to the visual standards required for the job. Of this group, 37 per cent had been involved in serious accidents, while 63 per cent had not. In the group who were below the visual standard required for the job, the figures were almost exactly reversed - 67 per cent had been involved in a serious accident, whereas 33 per cent had not.
Research has proved that the maintenance of a high standard of vision by the correction of visual defects is an important part of any accident prevention programme.
Environmental factors
There is little doubt, too, that an unsatisfactory environment from a visual point of view may be contributing factor in a considerable number of accidents, as well as giving rise to visual discomfort, fatigue, frustration and inefficiency. Often this is the result of poor or inadequate lighting, or lighting which illuminates the eyes of the worker more than the specific task and is, therefore, glaring.
If the lighting is inadequate the worker may be misinformed about the nature of objects, their position or the speed at which they may be moving. Tiredness may result because of strain, both physical and psychological. The presence of glare causes distraction or prevent essential details of the task from being seen.
Unfortunately much lighting in industrial premises is planned by people who have little formal lighting education. The more elementary mistakes can be avoided by ensuring that lighting decisions are taken by those with a good knowledge of at least the basic principles, and lighting conditions should be assessed for the various tasks to check that they are appropriate for the job to be performed efficiently. In the UK, the CIBSE Code for Interior Lighting gives recommendations on lighting levels recommended for various tasks and industries, and this should be consulted.
Visual efficiency
Most people who experience visual difficulties at work consult their own optometrist as soon as possible for advice and, where necessary, appropriate spectacles.
There are many workers, however, who are quite unaware that they have a visual problem which needs investigation and correction. This fact is highlighted again and again by surveys carried out in many countries which have established that about one-third of employees have vision below the standard required for their occupation. In many cases this is a result of uncorrected or insufficiently corrected visual defects which can affect efficiency, productivity and safety. It is also a cause for concern that up to a half of these people have spectacles which are so old that they would no longer be adequate to correct the defect for which they were prescribed.
Although much progress has been made in setting up various industrial safety schemes to protect the eyesight of the employee and ensuring that the protection demanded by legislation is provided and worn, the visual efficiency of the workers themselves is all too often neglected.
It is a sad fact that even today, far too often employees are hired and assigned to tasks on the basis of the employer’s needs or the supposed skills of the employee. In many cases few or no steps are taken to determine their visual abilities in relation to the job demands. Frequently the only, if any, eye test given to an employee or job applicant is a very crude test of distance vision - the eye function least used by the majority o industrial employees. Whilst this may be acceptable for less skilled workers not requiring critical vision, there are many others who, because of undetected or inadequately corrected visual defects, will be unable to perform their tasks with optimum efficiency, safety and comfort.
What is disturbing, however, is that people with defective eyesight are allowed to perform complicated and, in many cases, dangerous tasks simply because their sight is considered adequate to perform the task without having this confirmed by appropriate optometric tests.
Assessment of visual efficiency
Quite clearly, in the interests of both the employer and employee, a comprehensive visual assessment should form part of a pre-employment and training routine, followed up with periodic re-checks.
The importance of this is that:
- visual ability can be used in the selection of new employees or the identification of existing employees with visual disabilities. For those whose visual problems cannot be corrected, they can be transferred to a task in which they would be visually capable of performing efficiently
- improved visual efficiency can result in increased productivity, fewer accidents and therefore reduced insurance costs and reduced absenteeism, as the task is less visually demanding
- the recording of visual details at the beginning of employment provides the basis for evaluating problems which may arise later as a result of injury or disease where claims may be made for work-related loss of vision
- visual defects usually become more marked with time unless corrected and, therefore, it would be possible for an individual who is only just visually efficient when starting a new job from becoming increasingly inefficient the longer he remains at the job
- from a detailed knowledge of the work and working conditions advice can be given on methods of improving comfort and efficiency
- a professional assessment by an optometrist is an effective and reliable way of determining whether a worker’s vision is adequate in relation to the requirements and efficient performance of the task
Assessing the visual efficiency of employees may be carried out as part of a full eye examination by an optometrist or using a screening method.
It is first necessary to establish a visual standard for the task. This is may be a relatively straightforward procedure or, if the task is unique or highly complex, it may involve detailed analysis and assessment.
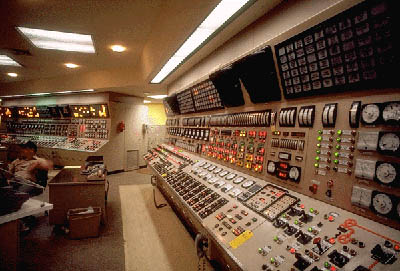
Establishing occupational visual standards
All jobs make varying demands on eyesight and it is essential that each worker should possess adequate vision for the work he is required to undertake. Some work requires the highest visual standards, such as those assembling delicate mechanisms or where there is an element of danger, whereas other jobs can be performed adequately by persons with relatively poor vision, for example, porters or caretakers. The train driver must have good colour appreciation to interpret signal colours as must a number of people in the electrical industry, yet this may be quite unimportant to others.
The airline pilot must have good stereoscopic vision but so must the crane operator to enable distances to be judged accurately. Although the worker with monocular vision is permitted to drive a motor car, he must be considered to be a risk to himself and others if he is asked to perform a job which involves working with moving machinery or where he would be especially liable to injury.
Some requirements are obvious and essential - others are more difficult to determine.
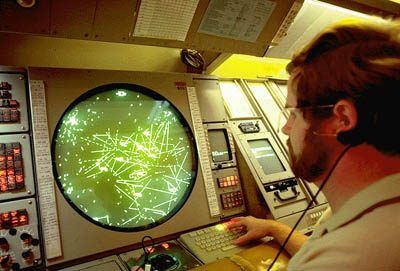
There are, of course, a number of occupations in which a minimum standard of vision is already predetermined and these are continually being reviewed, for example, air traffic control officers, airline pilots, professional drivers, visual display operators etc. Lists of standards of vision for various occupations may be found in the Association of Optometrists Members’ Handbook, the textbook ‘Work and the Eye’ by Rachel North, and other optical diaries.
All too often, however, no such standards exist and it then becomes necessary to establish the relationship between visual ability and job performance/competence by careful analysis of those attributes required to carry out a particular visual task effectively, as shown in Table 2.
Table 2. An indication of the type of information which is essential to an understanding of the visual demands placed on people by the nature of their work and hence the visual requirements necessary for efficiency and comfort.
Occupational Analysis
Name & General Description of Task |
Working Distances |
a. Far (Beyond 200cm)
b. Intermediate (200cm - 55cm)
c. Near (55cm - 30cm)
d. Very near (<30cm) |
Size of Detail |
a. Large (Angular size of critical detail over 10')
b. Medium (5' to 10')
c. Small (3' to 5')
d. Very small (2' to 3')
e. Extremely small (1' to 2')
f. Minute ( <1') |
Main Working Positions |
a. Sitting
b. Standing
c. Moving
d. Mixture |
Size of Working Areas (in which critical vision is required) |
a. Large
b. Medium
c. Small |
Head Movements |
a. Side to side
b. Up and down
c. Mixture) |
Direction of Gaze |
a. Ahead
b. Up
c. Down
d. Side
e. Mixture |
Changes in Direction of Gaze |
a. Frequent
b. Occasional
c. Seldom |
Movement of the Task |
a. Stationary
b. Slow movement
c. Fast |
Potential Danger |
a. High risk
b. Medium risk
c. Low risk |
Special Accuracy or Care |
a. Required
b. Limited requirements
c. Not required |
Binocular Vision and Stereoscopic Vision Requirements |
a. Required
b. Not important
c. Monocular vision adequate |
Colour Vision Requirement |
a. Good colour discrimination required
b. Limited requirements acceptable
c. Not required |
Visual Fields |
a. Good field required
b. Fair field acceptable
c. Poor |
Visibility (i.e. the relationship between the size of detail, working distances, contrast and time available for viewing the task) |
a. Good
b. Fair
c. Poor |
Type of lighting in use, its adequacy and suitability |
a. Good
b. Fair
c. Poor |
Hazard(s) |
a. Present (Identify and assess degree of risk)
b. Not present |
Eye Protection Requirements |
a. Required (select suitable PPE)
b. Not required |
Following analysis of the visual task, which allows the important visual factors to be determined, a standard can be set (after North 2001) by:
- Deciding on the criteria for visual competence, e.g. V.A. 6/9 or better, stereopsis, distinguish principal colours etc.
- Compare the vision of two groups of employees, age- and sex-matched if possible, who are judged to be: (a) job competent (b) job incompetent
- Compare their grading of visual competence to job competence. If the appropriate vision standard has been chosen, then the majority of the visually incompetent should fall into the job-incompetent group
- Alternatively, a normal level of visual capability for each factor can be made mandatory, e.g. VA 6/6 in each eye, normal colour vision etc. This approach would, of course, exclude some who may be perfectly capable of performing the task effectively
Summary
Every patient seen by an optometrist experiences wide and varied environments from, for example, a typical home or office, to the more unusual, unique industries and, although it is well known that visual factors have a vital influence on human activities, far too often, insufficient attention is given to determining the visual abilities of individuals and ensuring that they are capable of seeing in relation to the demands of particular tasks.
Anything which affects visual efficiency, such as a refractive error or muscle imbalance, or the nature of the task itself, such as fine detail or poor contrast or by the conditions under which the eyes must be used, such as poor lighting, must affect the efficiency of the individual.
In assessing occupational visual requirements, it is not sufficient to concentrate on any particular factor in isolation. The safest approach is to consider seeing as a whole, taking into account all of the relevant requirements which contribute to visual efficiency. This also requires an understanding and knowledge of the visual capability of the person, which will vary according to the demands of various tasks and between individuals performing the same task. For example, a myope may be able to carry out inspection work at close range without spectacles but would be severely handicapped if asked to drive a fork lift truck. Symptoms are likely to occur for VDU operators whose muscle imbalances are not well compensated, whereas others with identical, but well compensated heterophorias may be symptom free.
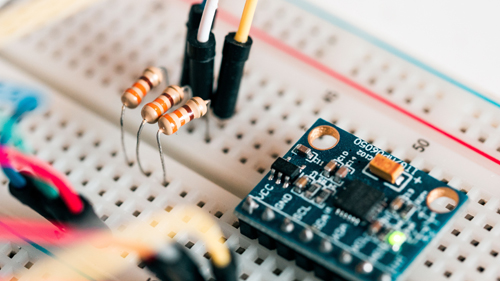
In modern industry there are now so many specialised and unusual occupations that analysing the visual factors involved in a task can often be difficult without visiting the place of work. In other cases, however, particularly where the optometrists is familiar with the occupation, useful information can be obtained by careful questioning in the consulting room.
Every occupation makes its own specific, characteristic visual demands which must be met before the task can be performed efficiently, safely and with comfort. The main aim of the optometrist, therefore, should be to gain a comprehensive knowledge and understanding of the visual demands likely to be made by the task and the environmental conditions in which it is carried out (task analysis), and to relate these to the visual ability of the worker to determine whether the task can be performed as well as possible. In some cases, direct assistance can be given, for example, in the form of spectacles, perhaps incorporating a correction specific for the task.
Advice should always be given on methods of making the task more visible or perhaps more comfortable. This will require an understanding and knowledge of (a) the influence of illumination (natural and artificial) and its effects on tasks and visual performance and (b) the use of colour and colour coding to improve visual performance and safety. The optometrist should also be aware of the factors which affect the visibility of a task and methods of improving visibility. This should include an awareness of the various light sources available and their characteristics and suitability for different tasks, the levels of lighting required for particular tasks and methods of measurement.
Advice on suitable and appropriate eye protectors may be given and this will require an awareness of the potential ocular hazards of various tasks, the types of hazards to which the eye is exposed, and a detailed knowledge of the responsibilities to a patient regarding the supply of eye protectors, the standards to which they are made and their identification.